Hot Work Steel: A Solid Foundation for High-Temperature Operations
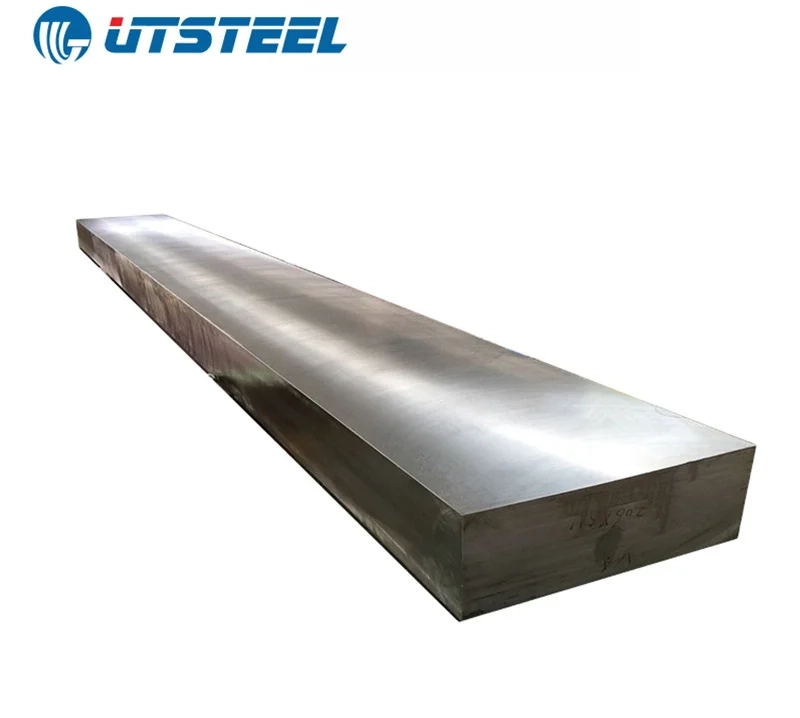
With the rapid development of modern industry, hot work steel has emerged as a key material in high-temperature processing, playing a vital role. It is widely used in fields such as metallurgy, mold manufacturing, automotive, aerospace, and more. Hot work steel's resistance to high temperatures, thermal fatigue, and excellent mechanical properties make it a “steel guardian” in high-temperature environments. In this article, UTSTEEL will discuss and analyze the basic characteristics and main application areas of hot work steel.
Basic Characteristics of Hot Work Steel
High Temperature Strength and Stability
The ability of hot work steel to perform under high-temperature conditions is mainly due to its exceptional high-temperature strength and thermal stability. In high-temperature environments, ordinary steel tends to soften, deform, or even fail. In contrast, hot work steel retains its hardness and strength at temperatures of hundreds or even thousands of degrees, thanks to its unique alloy design and metallurgical processes. This high-temperature strength allows hot work steel to maintain good mechanical properties, enabling it to withstand immense pressure and impact. It ensures the reliability and longevity of molds and tools used in processes like hot forging, stamping, and extrusion. For example, in hot forging dies, the steel must endure the enormous stress of metal forming at high temperatures. Hot work steel can operate for long periods in such environments without significant deformation or damage.
Thermal Fatigue Resistance and Thermal Stability
A major advantage of hot work steel is its excellent resistance to thermal fatigue. In high-temperature processes, tools and dies are frequently exposed to heating and cooling cycles. Rapid temperature fluctuations cause thermal stress within the material, leading to cracks or even fractures. This phenomenon, known as thermal fatigue, is one of the main causes of hot work tool failure. Through precise alloy composition design and stringent smelting control, hot work steel is engineered to withstand such temperature changes, minimizing the occurrence of thermal fatigue cracks. Its thermal stability at high temperatures allows it to maintain its physical and mechanical properties during continuous high- and low-temperature cycles, extending tool life, reducing production downtime, and lowering maintenance costs for enterprises.
Excellent Wear Resistance and Oxidation Resistance
Wear resistance is particularly critical for hot work steel in high-temperature processes. During high-temperature forming, friction between the tool and workpiece is intense, leading to continuous surface wear. If the material lacks sufficient wear resistance, the surface of the tool or mold will quickly degrade, negatively impacting production efficiency and product quality. By adding appropriate alloying elements (such as vanadium and molybdenum) and optimizing the heat treatment process, hot work steel forms a hard, wear-resistant surface even at high temperatures, greatly enhancing its wear resistance. Additionally, hot work steel exhibits good oxidation resistance. In high-temperature environments, ordinary steel can suffer from surface peeling or hardness reduction due to oxidation. Hot work steel resists high-temperature oxidation through the addition of antioxidant elements (such as chromium) and the use of specialized metallurgical techniques, ensuring that tools and molds maintain their performance in high-temperature conditions without significant oxidation-related degradation.
Main Application Areas of Hot Work Steel
Hot Forging Molds
Hot forging is a common metal processing method in which metal is heated to a certain temperature and plastically deformed in a mold by applying pressure to achieve the desired shape. During hot forging, molds must withstand extremely high temperatures and pressures, making the material choice critical. Hot work steel is the preferred material for hot forging molds due to its outstanding high-temperature strength and thermal fatigue resistance. In practical applications, hot work steel can endure the immense impact force and heat generated during metal forming, ensuring mold longevity and product quality. Its excellent wear resistance further reduces surface wear on molds, extending their service life.
Die Casting Molds
Die casting involves injecting molten metal into a mold cavity under high pressure, where it cools and solidifies rapidly. The molds in this process must withstand the rapid injection of high-temperature metal and the extreme temperature changes during cooling. Therefore, die casting molds require excellent thermal stability and resistance to thermal fatigue. Hot work steel is widely used in die casting molds, especially for metals such as aluminum and zinc alloys. It can resist the high-temperature erosion of molten metal and maintain consistent performance through repeated heating and cooling cycles. Moreover, hot work steel's high toughness and wear resistance ensure long-lasting mold performance, reducing the risk of cracking or wear, and thereby improving production efficiency.
Hot Extrusion Molds
In the hot extrusion process, heated metal materials are extruded through a die to form the desired shape. The molds in this process must withstand extremely high pressure and temperature, especially when shaping complex parts, where mold wear resistance and dimensional stability are crucial. The high-temperature strength and wear resistance of hot work steel make it an ideal choice for hot extrusion dies. It can endure the immense pressure exerted during metal extrusion while maintaining dimensional stability at high temperatures. By optimizing the heat treatment process, hot work steel exhibits exceptional durability and processing accuracy in hot extrusion molds.
With its exceptional high-temperature strength, thermal fatigue resistance, impact resistance, and wear resistance, hot work steel has become a fundamental material in modern high-temperature processing industries. In processes such as hot forging, die casting, and hot extrusion, hot work steel ensures the reliability and longevity of tools and molds. Furthermore, advanced heat treatment processes and surface treatments have further enhanced the performance of hot work steel, meeting the complex demands of industrial production.
https://www.gcmicgroup.com/Hot-Work-Steel-A-Solid-Foundation-for-High-Temperature-Operations.html
https://www.gcmicgroup.com/Hot-Work-Tool-Steel
www.gcmicgroup.com
UTSTEEL