Mining Internal Ring Gear: A Cornerstone of Mechanical Power Transmission in the Mining Industry
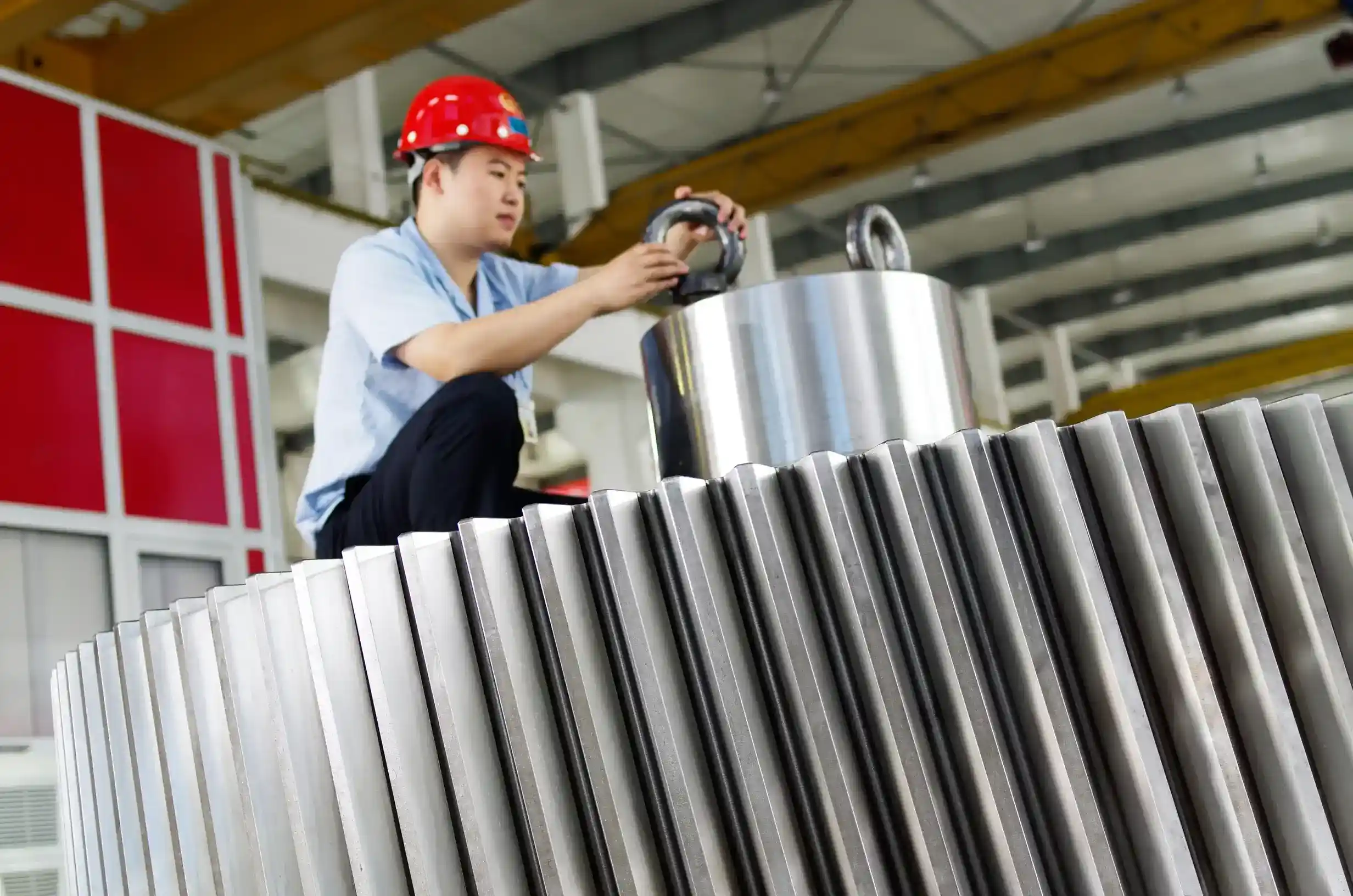
Mining internal ring gear, as a crucial component of transmission systems in mining equipment, directly influences the efficiency and reliability of the entire mechanical system. Due to its special structural design and sophisticated manufacturing process, mining internal ring gear has become an indispensable component in the mining industry. Especially in harsh and complex mining environments, the gear must withstand continuous high-intensity loads and frequent impacts, thereby demanding stringent technical performance and material properties. Whether in large open-pit mines or deep underground tunnels, the reliability and stability of mining internal ring gear ensure efficient and safe operations. Its strategic importance cannot be overstated, as failures or inefficiencies in this component can lead to substantial operational disruptions and financial losses.
Manufacturing Process of Mining Internal Ring Gear
The manufacturing process of mining internal ring gear is intricate and meticulous, involving three critical stages: forging, heat treatment, and gear shaping.
Forging Stage
In the forging stage, high-quality alloy steel or carbon steel is selected to ensure optimal mechanical strength and wear resistance. The raw material undergoes preheating, then is forged into rough ring shapes using ring rolling or die forging techniques. This process improves metal grain flow and eliminates internal voids, significantly enhancing the gear's structural integrity. Post-forging, the blanks are subjected to strict metallurgical inspections, including macro-structure testing, ultrasonic flaw detection, and dimensional verification, to prevent hidden defects that could compromise performance under load.
Heat Treatment Stage
Heat treatment is an essential step that fundamentally transforms the gear's physical properties. The sequence typically includes normalizing to relieve internal stresses, hardening via quenching, and then tempering to balance hardness and toughness. Advanced processes such as carburizing or nitriding are applied to increase surface hardness while retaining core ductility. These thermal cycles are carefully calibrated based on gear size, material, and intended application. Failure to maintain precise control can lead to issues like surface cracking or internal brittleness, which may result in premature failure during operation.
Gear Shaping Stage
Gear shaping is where the final precision and functional geometry of the mining internal ring gear are realized. Rough machining is followed by high-precision hobbing or shaping to cut the internal teeth. CNC grinding is then applied to achieve required surface finishes and tooth profile accuracies. Precision levels often reach IT6–IT7 class depending on operational demands. Micron-level deviations are not tolerated, as they directly affect transmission smoothness and load distribution. Post-machining treatments, such as deburring, surface coating, or cryogenic treatment, are also employed to improve wear resistance and fatigue strength. Final inspection using coordinate measuring machines (CMMs) ensures strict adherence to tolerance and design specifications.
Importance of Quality Control for Mining Internal Ring Gear
The complexity and critical function of mining internal ring gear necessitate rigorous quality control throughout the production lifecycle.
Raw Material and Pre-Production Testing: Each production batch begins with chemical composition analysis and mechanical testing of raw materials to verify compliance with specifications. Inclusion content, grain size, and tensile strength are examined using spectrometers and tensile testing machines. Only qualified materials proceed to the next stages.
Process Monitoring and In-Process Checks: Real-time monitoring during heat treatment ensures that the intended microstructure—typically a combination of martensite and tempered bainite—is achieved. Thermocouples and infrared imaging are used for temperature validation. During machining, inline dimensional inspections and tool wear monitoring are conducted to preempt production errors. Process capability indices (Cpk) are calculated to measure consistency.
Final Inspection and Validation: Once manufacturing is complete, the gear undergoes extensive final validation. This includes gear tooth contact pattern analysis, surface roughness measurements, hardness distribution mapping, and fatigue testing under simulated operational loads. 3D scanning and digital twin technology are increasingly used to compare manufactured components with design models, ensuring absolute fidelity to engineering intent.
Documentation and Traceability: Each gear is accompanied by a comprehensive quality dossier, including heat treatment curves, hardness profiles, inspection certificates, and flaw detection reports. This traceability is essential not only for quality assurance but also for warranty and future failure analysis if needed.
Mining internal ring gear stands out as a vital mechanical element underpinning the safe and efficient operation of modern mining equipment. From its robust material composition and precision engineering to its multifaceted applications in mission-critical systems, this component plays a pivotal role in the reliability of mining operations. Through a combination of advanced manufacturing techniques and unwavering quality control protocols, mining internal ring gear continues to meet the high expectations of the mining industry, driving productivity, safety, and cost-effectiveness in even the most extreme environments. Its importance will only increase as mining operations become more automated, integrated, and performance-driven.
https://www.tianshangear.com/Metallurgical-Building-Materials-and-Mining-Gear.html
www.tianshangear.com
Changzhou Tianshan Heavy Industry Machinery Co., Ltd.