Revolutionizing Comfort and Performance: The Rise of Industrial Workwear Stretch Fabric
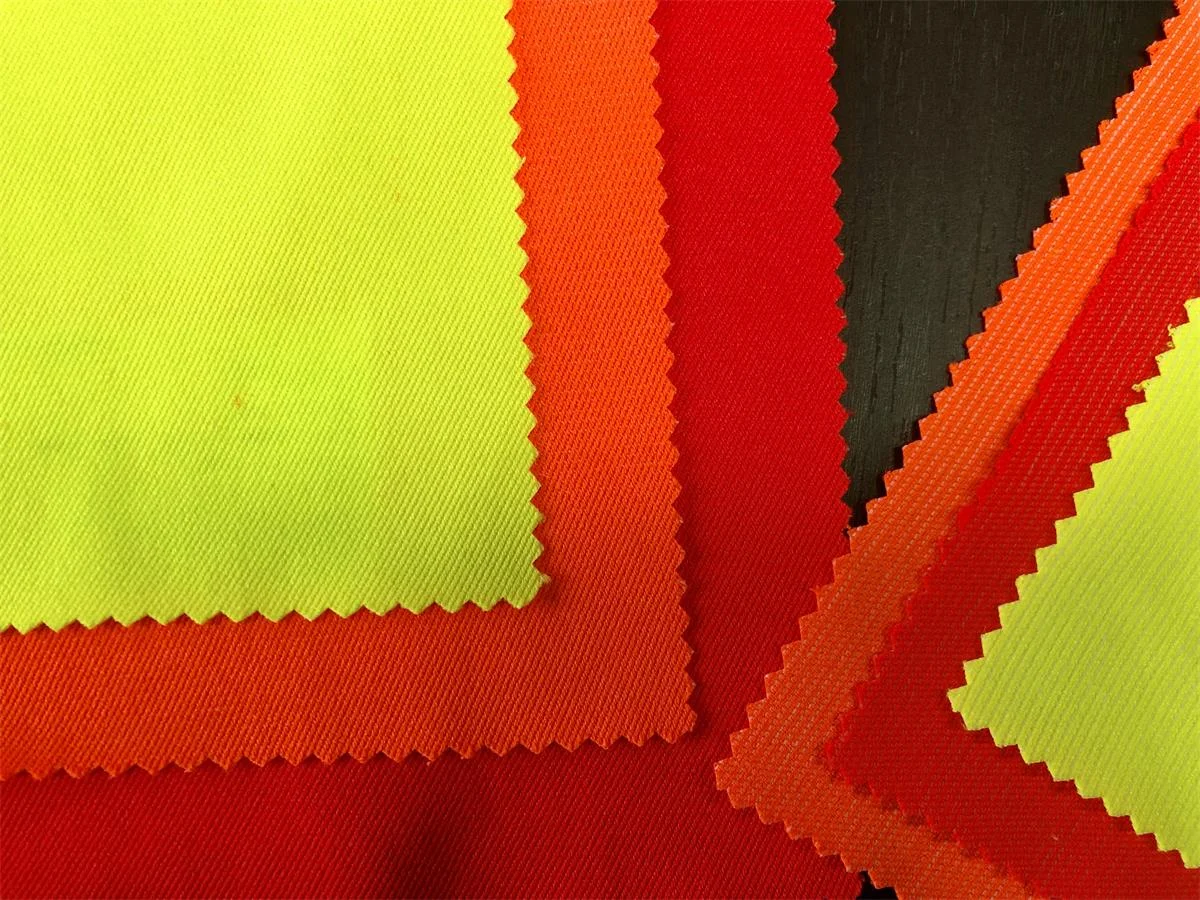
In today's fast-paced industrial environments, the demand for functional and comfortable workwear has never been higher. Workers are often required to perform physically demanding tasks that necessitate not only protection but also freedom of movement. Traditional fabrics can sometimes fall short, leading to discomfort and restricted mobility. Enter industrial workwear stretch fabric, a game-changing textile that combines innovative engineering with practical design. This fabric is tailored to meet the rigorous demands of various industries, enhancing both comfort and performance. This article Joy will explore the underlying technology of industrial workwear stretch fabric, illustrating why it has become an essential component in modern industrial apparel.
What is Industrial Workwear Stretch Fabric?
Industrial workwear stretch fabric is a specialized textile designed to facilitate both durability and flexibility for workers in various industrial sectors. Unlike traditional fabrics that may restrict movement, stretch fabrics are engineered to provide a high level of elasticity while maintaining strength and resilience. This is achieved through the integration of elastic fibers, such as spandex or elastane, into a blend of materials that often include cotton, polyester, and nylon.
The Technology Behind Industrial Workwear Stretch Fabric
The development of industrial workwear stretch fabric involves advanced textile technology that combines various materials and manufacturing processes to achieve desired performance characteristics. Here are some key technologies that play a role in the production of these fabrics:
1. Knitting and Weaving Techniques
The way industrial workwear stretch fabrics are constructed greatly influences their properties. Stretch fabrics can be made using different knitting or weaving techniques, such as warp knitting, circular knitting, or twill weaving. Each method affects the fabric's stretchability, breathability, and overall performance. For instance, warp-knitted fabrics typically provide more stretch in one direction, while circular knitted fabrics offer all-around flexibility. Understanding these techniques helps manufacturers tailor the fabric to meet specific performance requirements.
2. Fiber Blending
The blending of various fibers is a critical step in creating industrial workwear stretch fabric. By combining natural fibers like cotton with synthetic fibers such as polyester and spandex, manufacturers can produce fabrics that offer the best of both worlds—comfort and durability. This fiber blending allows for greater customization in terms of stretch, weight, and texture, tailoring the fabric to meet specific industry needs. Different blends can be engineered to enhance certain characteristics, such as moisture-wicking or abrasion resistance, depending on the intended use of the garment.
3. Finishing Treatments
Finishing treatments enhance the performance of industrial workwear stretch fabric by imparting additional properties. For example, water-repellent finishes can be applied to fabrics to create water-resistant workwear, while flame-retardant treatments are essential for safety in high-risk environments. Other treatments may include anti-microbial finishes to reduce odors or UV protection for outdoor applications. These finishing processes not only improve functionality but also help maintain the appearance and longevity of the fabric.
4. Moisture Management Technologies
Moisture management is a vital aspect of industrial workwear stretch fabric. Advanced moisture-wicking technologies enable fabrics to draw moisture away from the skin and transport it to the fabric's surface, where it can evaporate quickly. This feature is particularly beneficial in hot and humid environments, as it helps regulate body temperature and keeps the wearer comfortable. Manufacturers may also employ hydrophilic and hydrophobic fibers to create a fabric that efficiently manages moisture, ensuring that workers stay dry and focused on their tasks.
5. Advanced Testing and Quality Control
The production of industrial workwear stretch fabric involves rigorous testing and quality control measures to ensure that the final products meet industry standards. Tests may include evaluations of tensile strength, abrasion resistance, colorfastness, and comfort properties. Manufacturers utilize advanced equipment and methodologies to guarantee that the fabric performs reliably in real-world conditions. This commitment to quality assurance is crucial for maintaining trust with customers and ensuring that workers have access to dependable and effective workwear.
Industrial workwear stretch fabric is revolutionizing the way work apparel is designed and utilized across various industries. Its unique combination of comfort, flexibility, and durability makes it an ideal choice for environments that demand high-performance clothing. By incorporating advanced textile technologies, industrial workwear stretch fabric offers solutions that enhance worker comfort, productivity, and safety in diverse applications, from manufacturing and construction to healthcare and hospitality. The continued development and adoption of this innovative fabric will play a crucial role in shaping the future of industrial apparel, ensuring that workers are equipped with the best possible garments to meet their challenging roles.
https://www.szjoyfabric.com/Workwear-Industrial-with-Stretch
www.szjoyfabric.com
Suzhou Joy P&D