What are the causes of feed mixer leakage?
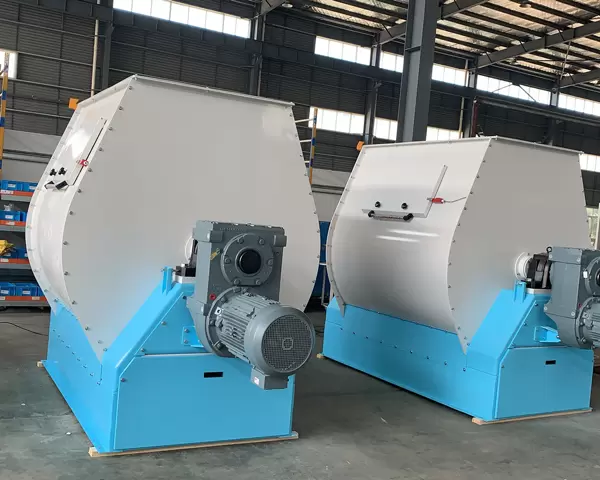
In animal husbandry production, feed mixer is one of the indispensable equipment. Its function is to mix a variety of raw materials evenly to provide balanced nutrition to livestock. However, in actual use, leakage problems of feed mixers occur from time to time, which not only affects the quality of feed, but also may cause waste of resources. This article will discuss in detail the causes of feed mixer leakage and propose corresponding solutions.
1. Common causes of feed mixer leakage
Failure of mechanical seal
Aging of seals: Mechanical seals are one of the key components of feed mixers, which play a role in preventing material leakage. However, as the use time increases, the seals will gradually age, lose their original elasticity and sealing performance, resulting in leakage.
Improper installation
If the mechanical seal is improperly installed, such as uneven sealing surface and uneven force on the fastening bolts, it will lead to poor sealing effect, which will cause leakage.
Severe wear: During long-term operation, the mechanical seal will be gradually worn by friction and impact of the material. When worn to a certain extent, the sealing performance will be greatly reduced or even completely ineffective.
Wear or deformation of the mixing blade
High material hardness: If the material being mixed has a high hardness, such as containing more impurities such as sand and gravel, it will cause serious wear on the mixing blade. After the blade is worn, its mixing effect will decrease, and it will also damage the sealing structure of the mixer, causing leakage.
High impact force: In some cases, the impact force when the material enters the mixer is large, which may cause the mixing blade to deform. The deformed blade will not only affect the mixing effect, but also may cause a gap with the inner wall of the mixer, causing leakage.
Damage to the mixer shell
Corrosion: Feed mixers usually work in a humid environment and are susceptible to corrosion. If the shell material of the mixer is not corrosion-resistant enough or the anti-corrosion measures are not in place, corrosion perforation may occur, causing leakage.
External force impact: During transportation or use, the mixer may be hit by external force, causing the shell to deform or rupture. In this case, leakage problems are likely to occur.
Bearing damage
Poor lubrication: Bearings are an important part of feed mixers. If they are poorly lubricated, the bearings will wear more and even burn out. When the bearing is damaged, it will affect the normal operation of the mixer and may also cause leakage.
Overload operation: If the mixer is overloaded for a long time, it will bring excessive load to the bearing and accelerate the damage of the bearing. After the bearing is damaged, it may cause vibration and noise of the mixer, which will lead to leakage.
2. Countermeasures to solve the leakage of feed mixer
Strengthen maintenance
Check the seals regularly: Check the mechanical seals regularly and replace them in time if they are aging, worn, etc. At the same time, when installing the seals, ensure that the sealing surface is flat and the fastening bolts are evenly stressed.
Check the mixing blades: Check the wear of the mixing blades regularly, and repair or replace them in time if necessary. In addition, pay attention to controlling the hardness and impact force of the material to avoid excessive wear on the blades.
Maintain the bearings: Lubricate and maintain the bearings regularly to ensure the good operating condition of the bearings. At the same time, avoid long-term overload operation of the mixer to reduce the load on the bearings.
Improve the quality of equipment
Choose high-quality materials: When choosing a feed mixer, give priority to equipment made of high-quality materials that are corrosion-resistant and wear-resistant. This can improve the durability and reliability of the equipment and reduce the risk of leakage.
Optimize design: optimize the structure of the feed mixer, such as adding reinforcement ribs, improving the sealing structure, etc., to improve the impact resistance and sealing performance of the equipment.
Standardize the operation process
Operate the equipment correctly: operate strictly in accordance with the operating procedures of the equipment to avoid equipment damage and leakage due to improper operation. For example, before starting the mixer, make sure that the material is evenly distributed in the mixing drum; when stopping the mixer, wait until the material is emptied before turning off the power.
Strengthen training: provide professional training for operators to improve their operating skills and safety awareness. Let the operators understand the working principle of the equipment and common troubleshooting methods so that they can take timely measures when problems arise.
Feed mixer leakage is a complex problem involving multiple factors. To solve this problem, it is necessary to start with strengthening maintenance, improving equipment quality, standardizing operating procedures and establishing a monitoring system. Only by comprehensively considering and taking effective measures can we ensure the normal operation of the feed mixer, improve production efficiency, reduce production costs, and contribute to the development of animal husbandry. At the same time, we should also continue to pay attention to the development and application of new technologies and actively explore more advanced solutions to further improve the performance and reliability of feed mixers.
As a professional feed mixer exporter, we are well aware that the quality and performance of our equipment are of vital importance to our customers. Feed mixers play a key role in animal husbandry production, so we are always committed to providing high-quality feed mixers. At the same time, we also focus on standardizing operating procedures, providing professional training for customers, ensuring the correct use of equipment, and contributing to the development of the global animal husbandry industry.
https://www.fast-js.com/
Jiangsu FAST Intelligent Equipment Co., Ltd.