Will extreme environments affect the performance of line tube condensers?
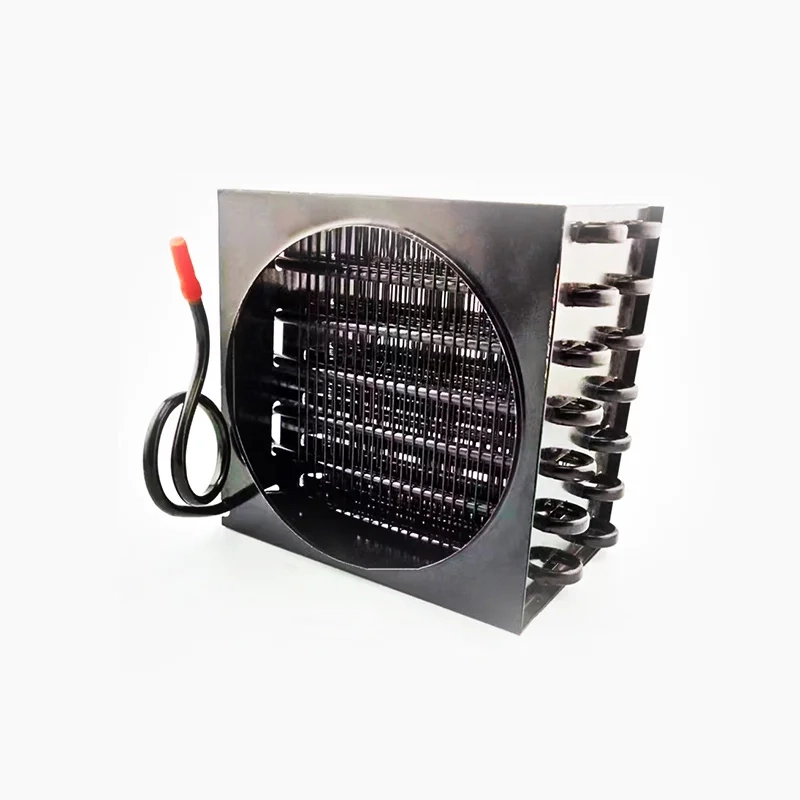
In many industrial applications, wire-tube condensers play a key role, especially those that require equipment to continue to operate stably in extreme environments. From extremely low-temperature refrigeration environments to high-temperature and high-pressure processes, wire-tube condensers must have excellent durability and reliability. This article will explore the performance of wire-tube condensers in various extreme environments, including their design features, material selection, and how to meet stringent application requirements through technological innovation.
1. Performance in extreme temperature environments
Extreme temperature conditions pose challenges to the material and structural design of wire-tube condensers. In low-temperature environments, materials may become brittle, leading to rupture; while at high temperatures, it is necessary to prevent material strength from decreasing and deformation caused by thermal expansion. For these situations, wire-tube condensers usually use special alloy materials or specially heat-treated metals to maintain their mechanical stability and corrosion resistance over a wide temperature range. In addition, the choice of insulation material is also crucial, as it must be able to withstand the thermal stresses caused by extreme temperature differences.
2. Anti-corrosion and chemical stability
In many extreme environments, such as marine, chemical and oil platforms, wire-tube condensers need to have superior corrosion resistance. Under these conditions, the condenser may be exposed to highly salty water, acidic gases, or other corrosive chemicals. Therefore, the surface treatment and material selection of line pipes are particularly important. Usually, stainless steel, titanium or nickel-based alloys can effectively improve corrosion resistance. At the same time, the contact between the corrosive medium and the metal surface can be further isolated through coating techniques such as chromium plating or the application of special non-metallic coatings.
3. High pressure and mechanical stress
Wire-tube condensers working in some high-pressure environments need to withstand huge mechanical stress. This not only requires that the line pipe be thick enough to resist deformation caused by pressure, but also requires that the supporting structure be strong enough to prevent collapse or breakage. For this reason, reinforced support structure and optimized mechanical design have become key factors to ensure the long-term stable operation of wire-tube condensers in such an environment.
4. Vibration and dynamic load
In some extreme applications, such as condensers on offshore platforms or transportation vehicles, the vibration problem of the equipment cannot be ignored. Continuous dynamic loads can cause fatigue damage and reduce equipment service life. In order to alleviate this problem, the design of wire-tube condensers often includes anti-vibration devices and flexible joints, as well as determining the natural frequency through modal analysis to avoid the occurrence of resonance phenomena.
5. Maintenance strategies in extreme environments
In extreme environments, wire-tube condensers require regular maintenance to ensure their performance is not affected. This includes regular inspections for potential corrosion points, monitoring temperature and pressure indicators, and prompt cleaning of dirt and deposits. Maintenance work not only requires professional technical support, but also requires special consideration on how to operate safely and efficiently in harsh environments.
6. Innovation and future trends
With the development of science and technology, new materials and new technologies are constantly being developed to improve the performance of wire-tube condensers in extreme environments. For example, the application of nanotechnology is improving heat transfer efficiency and corrosion resistance, while advanced monitoring systems enable real-time performance tracking. Future wire-tube condensers are expected to become more intelligent and adaptive, able to adjust their working status in changing external environments to maximize efficiency and longevity.
Extreme environments pose a unique set of challenges to wire-tube condensers, involving material selection, design optimization, anti-corrosion measures and maintenance strategies. Through continuous technological innovation and in-depth engineering research, modern wire-tube condensers have been able to meet the working requirements under a variety of harsh conditions. With the development and application of new technologies, wire-tube condensers will continue to improve their performance in extreme environments in the future to meet growing industrial needs.
Deciphering the wire-tube condenser: the secrets of its structure and components
Wire-tube condenser is an environmentally friendly tool in refrigeration equipment
Customized wire-tube condenser, the future trend of efficient refrigeration
Optimized design: key steps to create an efficient wire-tube condenser
Wire-tube condenser safety and reliability analysis: influencing factors and improvement strategies
The development history of wire-tube condenser
An in-depth discussion on the heat exchange efficiency of wire-tube condenser
wire-tube condenser installation and debugging guide
Corrosion resistance, selection and application of wire-tube condenser materials
Impact and application analysis of wire-tube condenser on energy efficiency
How to clean and maintain wire-tube condenser?
How to choose refrigerant for wire-tube condenser
Analysis of the role and importance of wire-tube condensers in refrigeration system
Heat dissipation performance analysis and optimization strategies of wire-tube condensers
The role of wire-tube condensers in air conditioning systems
Heat conduction characteristics of wire-tube condensers
How to effectively prevent corrosion of wire-tube condensers
Application of wire-tube condensers in environmental protection
mia
Lon@ningbo-senjun.com