PLC vs DCS: Unveiling the Distinctions and Applications
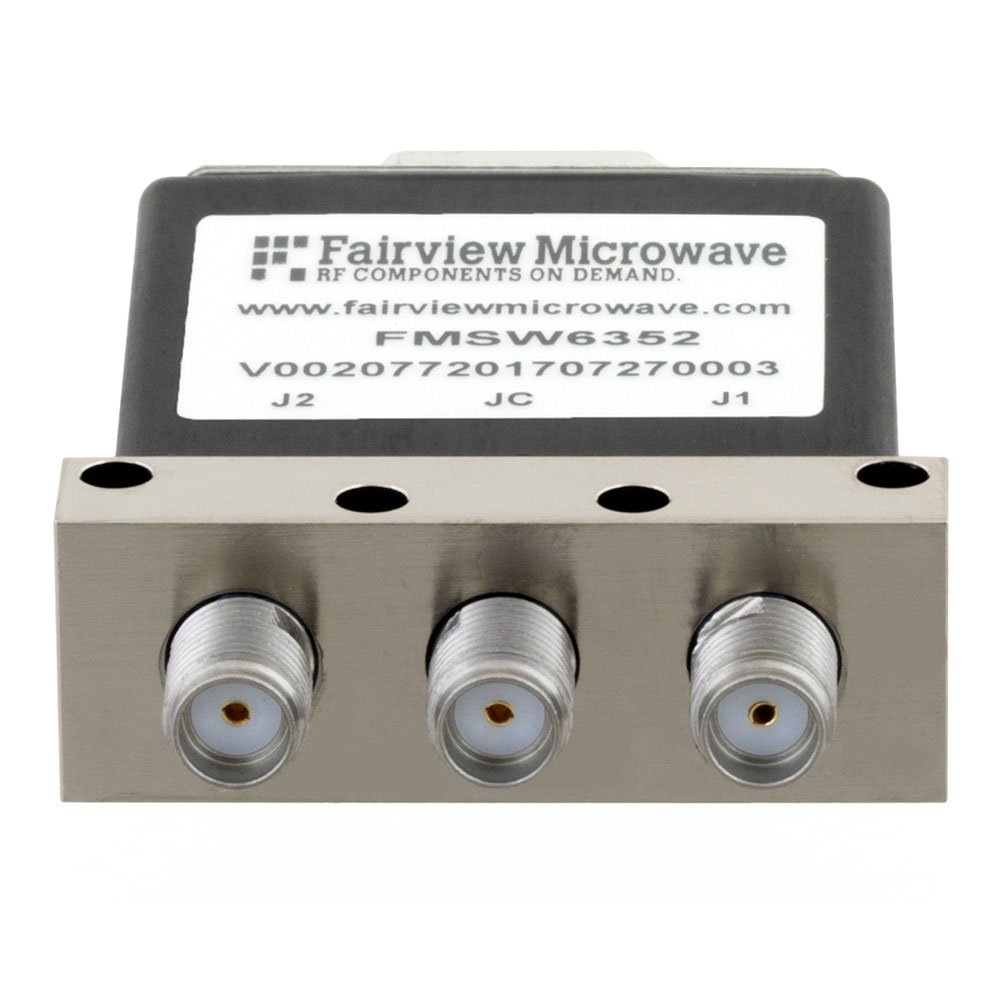
In the realm of industrial automation, two prominent control systems have emerged as key players: Programmable Logic Controllers (PLCs) and Distributed Control Systems (DCS). While both serve the purpose of controlling and monitoring industrial processes, they differ significantly in their architecture, functionality, and application scope. In this article, we will delve into the intricacies of PLCs and DCS, exploring their differences and shedding light on their respective applications.
- Architecture:
PLCs: Programmable Logic Controllers are compact, standalone devices designed for discrete control applications. They consist of a central processing unit (CPU), input/output modules, and a programming interface. PLCs are typically programmed using ladder logic or other programming languages, allowing for flexible and customizable control logic.
DCS: Distributed Control Systems, on the other hand, are characterized by a distributed architecture. They comprise multiple interconnected controllers, each responsible for a specific process area. These controllers communicate with a central server, enabling seamless integration and coordination across the entire system. DCSs are commonly programmed using proprietary software, offering advanced control algorithms and extensive data processing capabilities.
- Functionality:
PLCs: PLCs excel in discrete control applications, where the process involves discrete events or on/off control. They are widely used in industries such as manufacturing, automotive, and packaging. PLCs offer fast response times, high reliability, and precise control over individual components or machines. They are ideal for applications that require sequential logic, such as conveyor belt control or robotic assembly lines.
DCS: Distributed Control Systems are tailored for continuous control applications, where the process involves continuous variables and analog signals. DCSs find extensive use in industries such as oil and gas, power generation, and chemical processing. With their distributed architecture, DCSs can handle complex processes spanning multiple control loops. They provide advanced control algorithms, data acquisition, and analysis capabilities, enabling operators to optimize process efficiency and ensure safety.
- Scalability:
PLCs: PLC systems are highly scalable, allowing for easy expansion and modification. Additional input/output modules can be added to accommodate new devices or sensors, making them suitable for small to medium-sized applications. PLCs offer a cost-effective solution for controlling individual machines or small production lines.
DCS: Distributed Control Systems are designed for large-scale applications, offering scalability to handle complex and extensive processes. With their distributed architecture, DCSs can seamlessly integrate thousands of control loops, enabling centralized monitoring and control of an entire plant or facility. DCSs are ideal for industries that require extensive process coordination and optimization.
Conclusion:
In summary, while both PLCs and DCSs serve the purpose of industrial control, their differences lie in architecture, functionality, and scalability. PLCs excel in discrete control applications, providing precise control over individual components, while DCSs are tailored for continuous control applications, offering advanced control algorithms and extensive data processing capabilities. Understanding these distinctions is crucial for selecting the appropriate control system for specific industrial requirements.