Unveiling the Drawbacks of Relays in PLC Systems
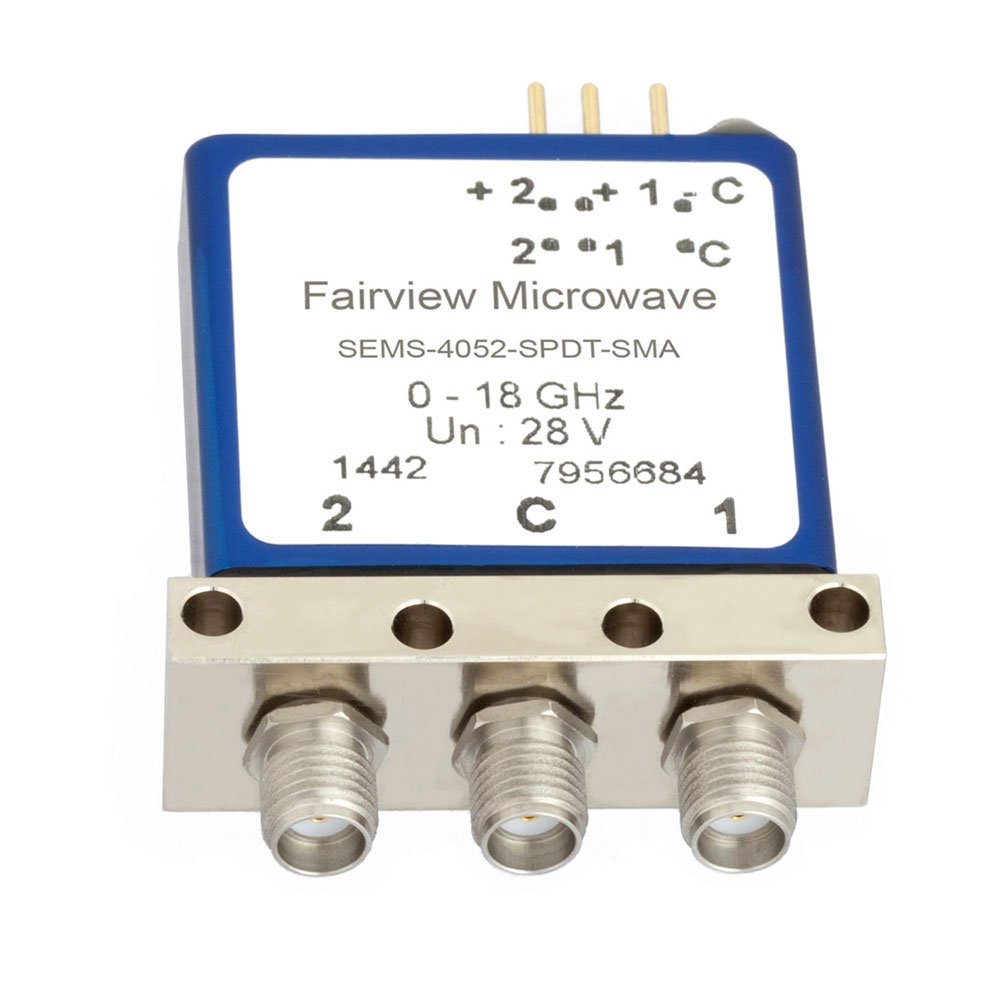
In the world of industrial automation, Programmable Logic Controllers (PLCs) play a crucial role in controlling and monitoring various processes. While PLCs offer numerous advantages, it is essential to acknowledge the potential disadvantages of using relays within these systems. This article aims to explore the drawbacks associated with relays in PLCs, shedding light on their limitations and providing insights into alternative solutions.
- Limited Switching Speed:
Relays, as electromechanical devices, have inherent mechanical components that introduce a delay in the switching process. This delay can lead to slower response times, which may be critical in applications requiring high-speed operations. For instance, in industries such as automotive manufacturing or packaging, where precise timing is crucial, the sluggish switching speed of relays can hinder overall system performance. - Reduced Reliability:
Due to their mechanical nature, relays are subject to wear and tear over time. The constant movement of mechanical parts can lead to mechanical failures, resulting in system downtime and increased maintenance costs. Moreover, the contacts within relays can experience arcing and pitting, leading to contact degradation and potential signal loss. These reliability concerns make relays less suitable for applications demanding continuous and uninterrupted operation. - Limited Lifespan:
Relays have a finite lifespan, primarily determined by the number of switching cycles they can endure. Frequent switching operations can significantly reduce their operational life, necessitating frequent replacements. This not only adds to the maintenance costs but also increases the risk of unexpected failures, potentially disrupting critical processes. In contrast, solid-state devices, such as transistors or semiconductor switches, offer virtually unlimited switching cycles, making them a more reliable alternative. - Size and Space Constraints:
Relays, being bulky electromechanical devices, occupy a considerable amount of space within control panels or cabinets. In applications where space is limited, such as in compact machinery or control systems, the size of relays can pose challenges. Additionally, the larger size of relays can lead to increased wiring complexity, making installation and troubleshooting more time-consuming and cumbersome. - Limited Flexibility and Scalability:
Relays are typically designed for specific voltage and current ratings, limiting their flexibility in adapting to varying system requirements. Upgrading or modifying a relay-based PLC system to accommodate higher loads or different voltage levels often requires replacing the entire relay module, resulting in additional costs and downtime. In contrast, solid-state devices offer greater flexibility, allowing for easier scalability and customization without the need for extensive hardware changes.
Conclusion:
While relays have been widely used in PLC systems for many years, it is crucial to recognize their limitations and consider alternative solutions. The drawbacks of relays, including limited switching speed, reduced reliability, finite lifespan, size constraints, and limited flexibility, can impact system performance and increase maintenance costs. By exploring alternative technologies, such as solid-state devices, industrial automation can achieve higher efficiency, reliability, and adaptability, ultimately driving progress in various industries.