Material selection for deep groove ball bearings
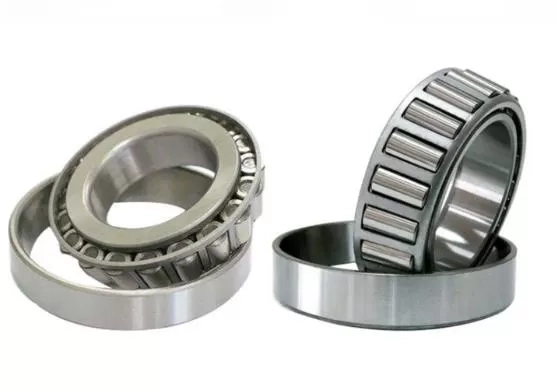
Deep groove ball bearings are a common bearing type and are widely used in mechanical equipment in various fields. In the design and manufacturing process of deep groove ball bearings, material selection plays a vital role. This article will discuss the material selection of deep groove ball bearings, explore the impact of different materials on bearing performance and how to choose appropriate materials.
First of all, the material selection of deep groove ball bearings needs to take into account its requirements under working conditions, including load, speed, temperature and environment. Common deep groove ball bearing materials include steel, ceramics and plastics.
Steel is the most commonly used material for deep groove ball bearings and has good strength and wear resistance. Steel materials are usually made of high carbon chromium steel (GCr15) or stainless steel (such as AISI 440C). High carbon chromium steel has high hardness and strength and is suitable for bearings with high load and high speed operation. Stainless steel has good corrosion resistance and is suitable for bearing applications in humid or corrosive environments.
Ceramic materials are increasingly used in deep groove ball bearings. Ceramic bearings have low friction coefficient, high hardness and corrosion resistance, and are suitable for working conditions at high speeds, high temperatures and special environments. Common ceramic materials include alumina (Al2O3), silicon nitride (Si3N4) and silicon carbide (SiC). These materials have excellent mechanical and thermal properties and can meet the requirements under special working conditions.
Plastic materials are also used in the manufacture of deep groove ball bearings in special applications. Plastic bearings have good corrosion resistance, self-lubricating and shock-absorbing properties, and are suitable for bearing applications with low loads and low speeds. Common plastic materials include polytetrafluoroethylene (PTFE), polyimide (PI) and polyamide (PA). These materials have good wear resistance and chemical resistance and can meet the requirements of some special working conditions.
When selecting deep groove ball bearing materials, the working conditions and performance requirements of the bearing need to be comprehensively considered. First, working conditions such as load and rotational speed need to be determined to select the appropriate material. For bearings with high loads and high speeds, high carbon chromium steel or ceramic materials are usually chosen. Secondly, the operating temperature and environment of the bearing need to be considered, and materials with good heat resistance and corrosion resistance need to be selected. Finally, you also need to consider factors such as cost and availability to select economical and practical materials.
In summary, the material selection of deep groove ball bearings has an important impact on bearing performance and life. Different materials such as steel, ceramics and plastics have their own advantages and scope of application. When selecting materials, factors such as working conditions, performance requirements, and economic practicality need to be comprehensively considered. Through reasonable selection of materials, the performance and reliability of deep groove ball bearings can be improved to meet the needs of different working conditions.
mia
amy@dejin-inc.com