Solving the Mystery of Mechanical Seal Leaks
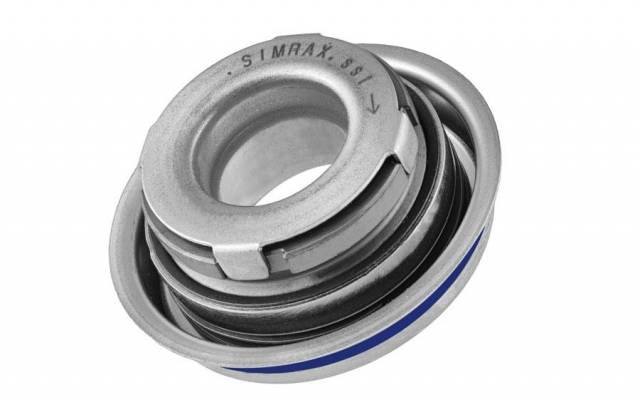
Mechanical seals are critical components in many industrial applications, including pumps, compressors, and mixers. They are designed to prevent the leakage of fluids and gases from the equipment, ensuring safe and efficient operation. However, despite their importance, mechanical seals can sometimes fail, leading to leaks that can cause significant damage and downtime. In this blog post, we will explore the reasons why mechanical seals leak and provide practical solutions to prevent and address these issues.
- Poor Installation
One of the most common reasons for mechanical seal leaks is poor installation. If the seal is not installed correctly, it can cause misalignment, excessive vibration, and premature wear, leading to leaks. To prevent this issue, it is essential to follow the manufacturer's installation instructions carefully and ensure that the seal is properly aligned and lubricated.
- Wear and Tear
Mechanical seals are subject to wear and tear over time, especially in high-pressure and high-temperature applications. The seal faces can become scratched, pitted, or worn, leading to leaks. Regular maintenance and inspection can help identify and address these issues before they cause significant damage.
- Contamination
Contamination is another common cause of mechanical seal leaks. Dirt, debris, and other particles can enter the seal and cause damage to the seal faces, leading to leaks. To prevent this issue, it is essential to keep the equipment clean and free of debris and to use appropriate filtration systems.
- Improper Material Selection
The selection of the wrong materials for the mechanical seal can also cause leaks. Different applications require different materials, and using the wrong material can lead to premature wear and failure. It is essential to consult with the manufacturer or a qualified engineer to ensure that the correct materials are selected for the specific application.
- Operating Conditions
The operating conditions of the equipment can also contribute to mechanical seal leaks. High temperatures, pressures, and speeds can cause excessive wear and tear on the seal faces, leading to leaks. It is essential to monitor the operating conditions and adjust them as necessary to prevent damage to the mechanical seal.
In conclusion, mechanical seal leaks can be caused by a variety of factors, including poor installation, wear and tear, contamination, improper material selection, and operating conditions. By understanding these issues and taking appropriate measures to prevent and address them, it is possible to ensure safe and efficient operation of industrial equipment. Regular maintenance, inspection, and consultation with qualified engineers can help identify and address these issues before they cause significant damage and downtime.